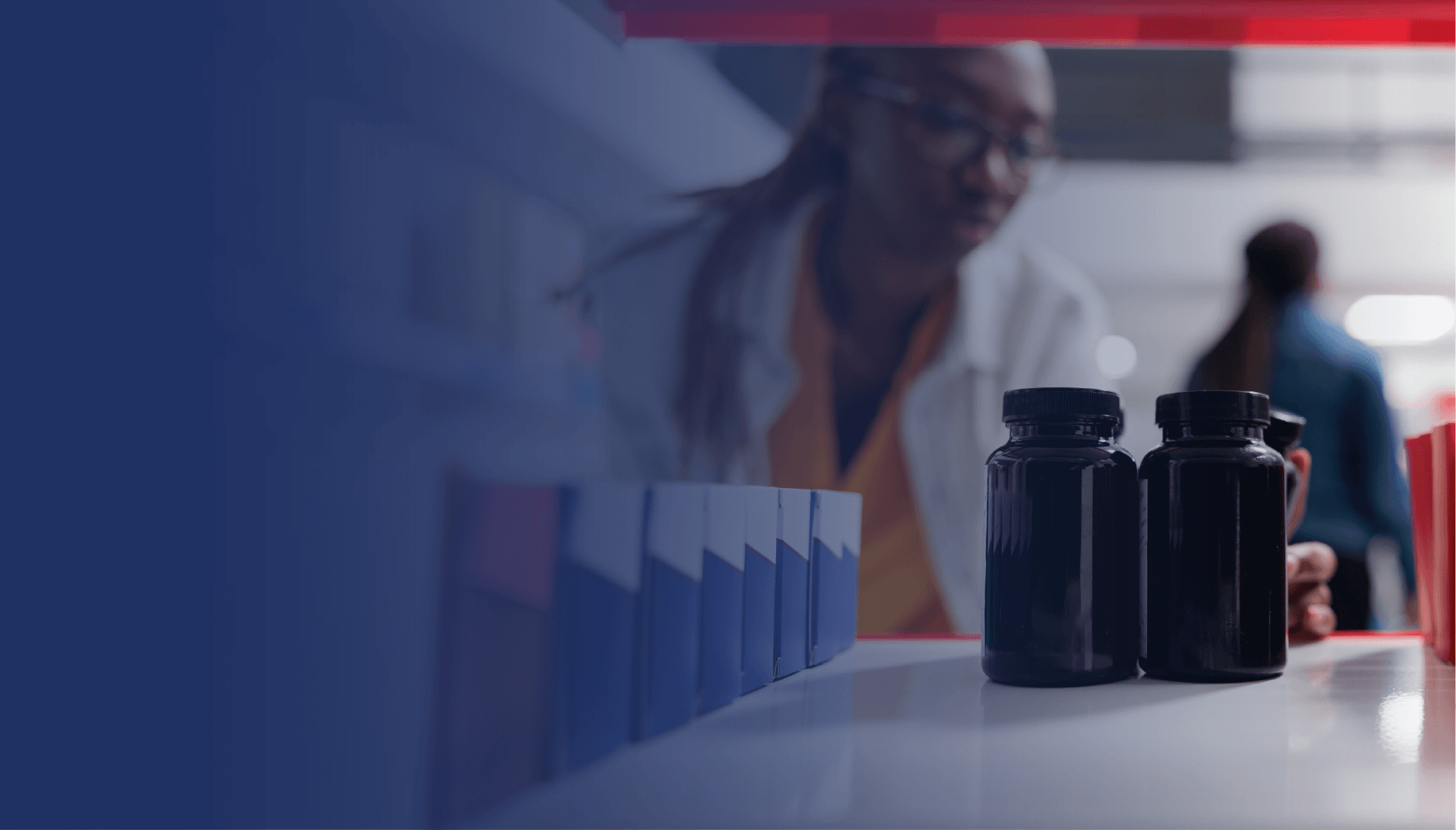
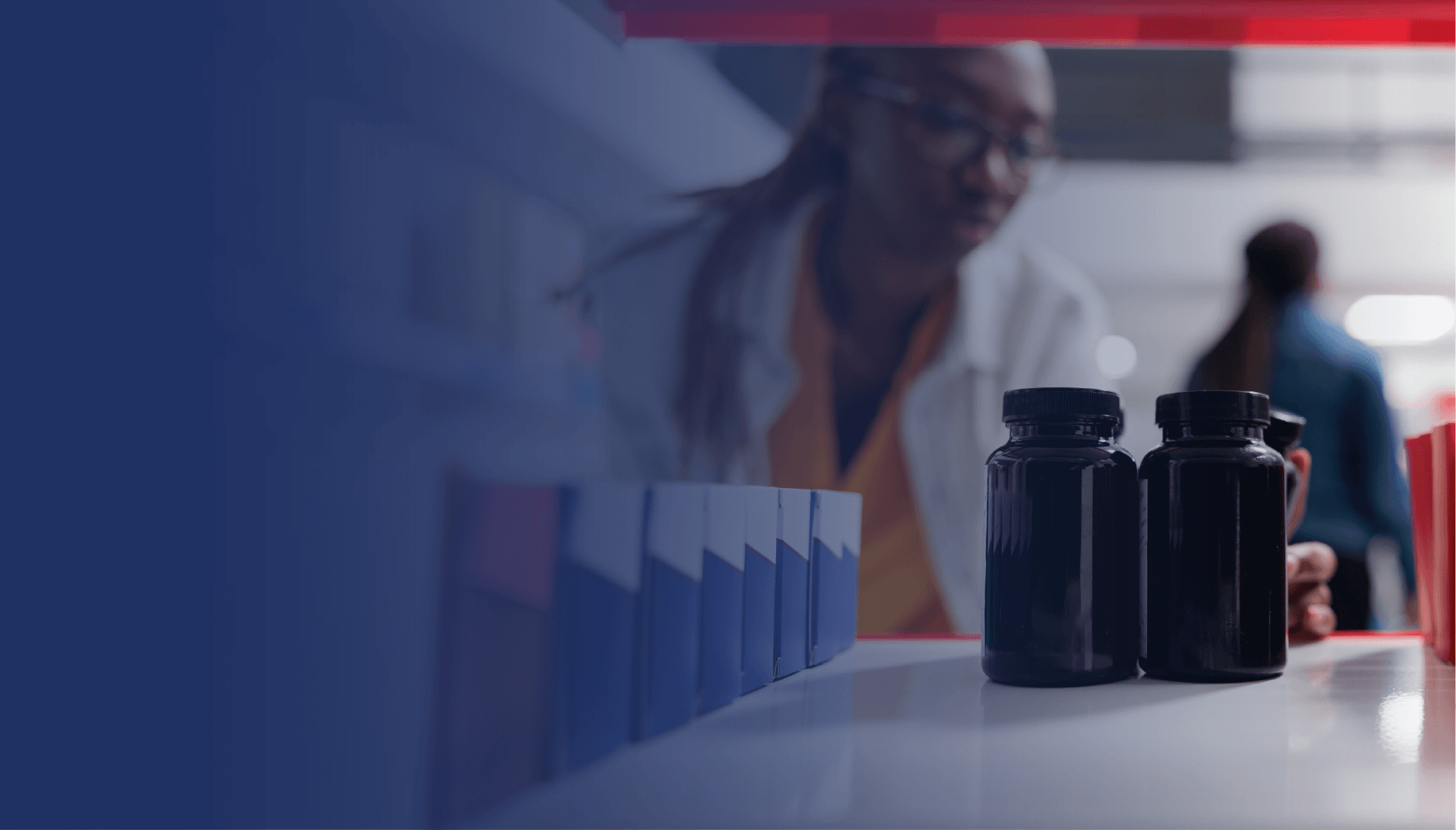
Our Process
‘Ideation to Creation’
with our expert team.
We partner with our clients to ensure a streamlined and efficient process for all product orders.
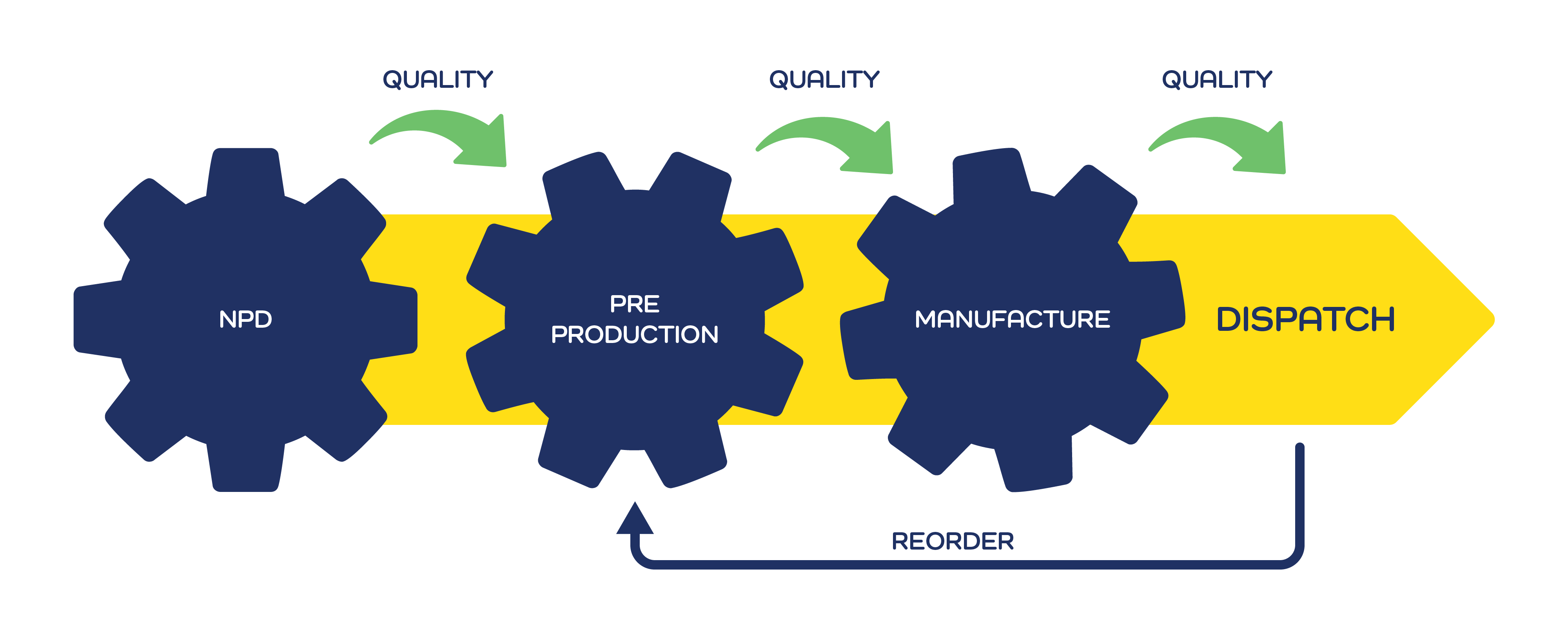
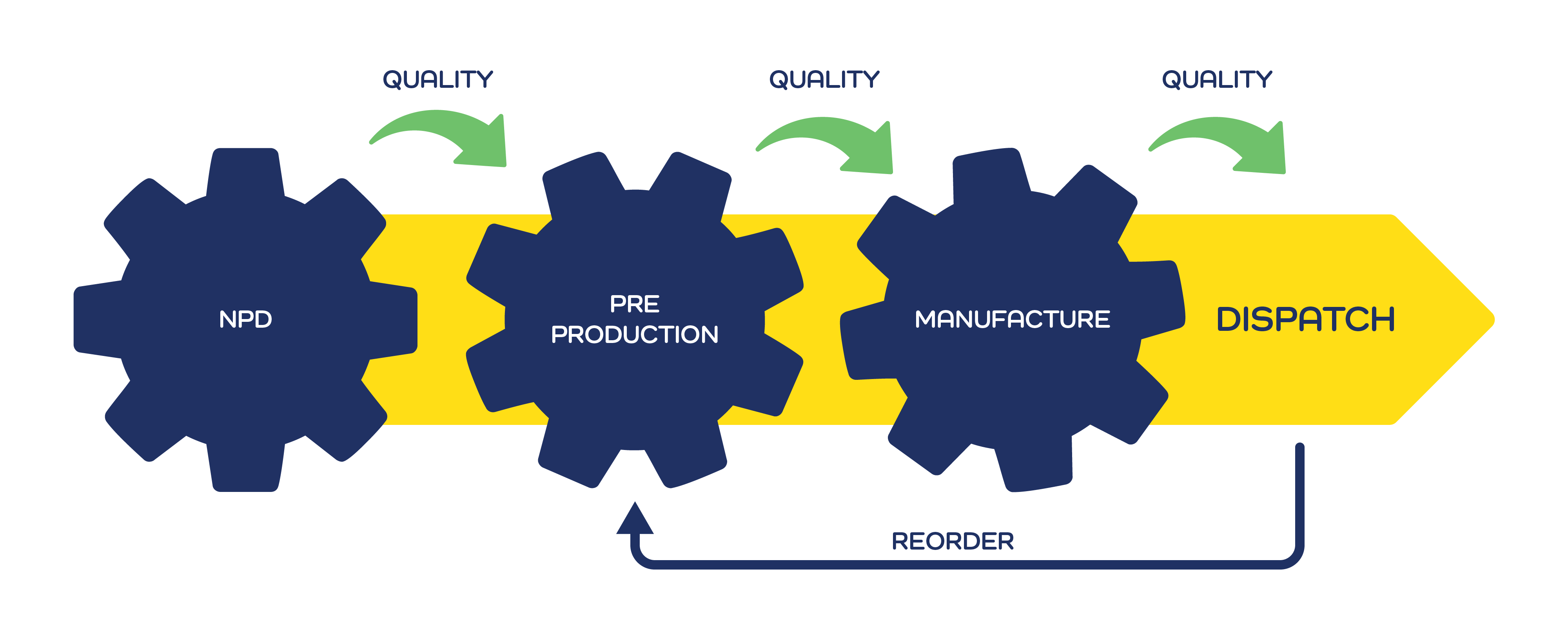
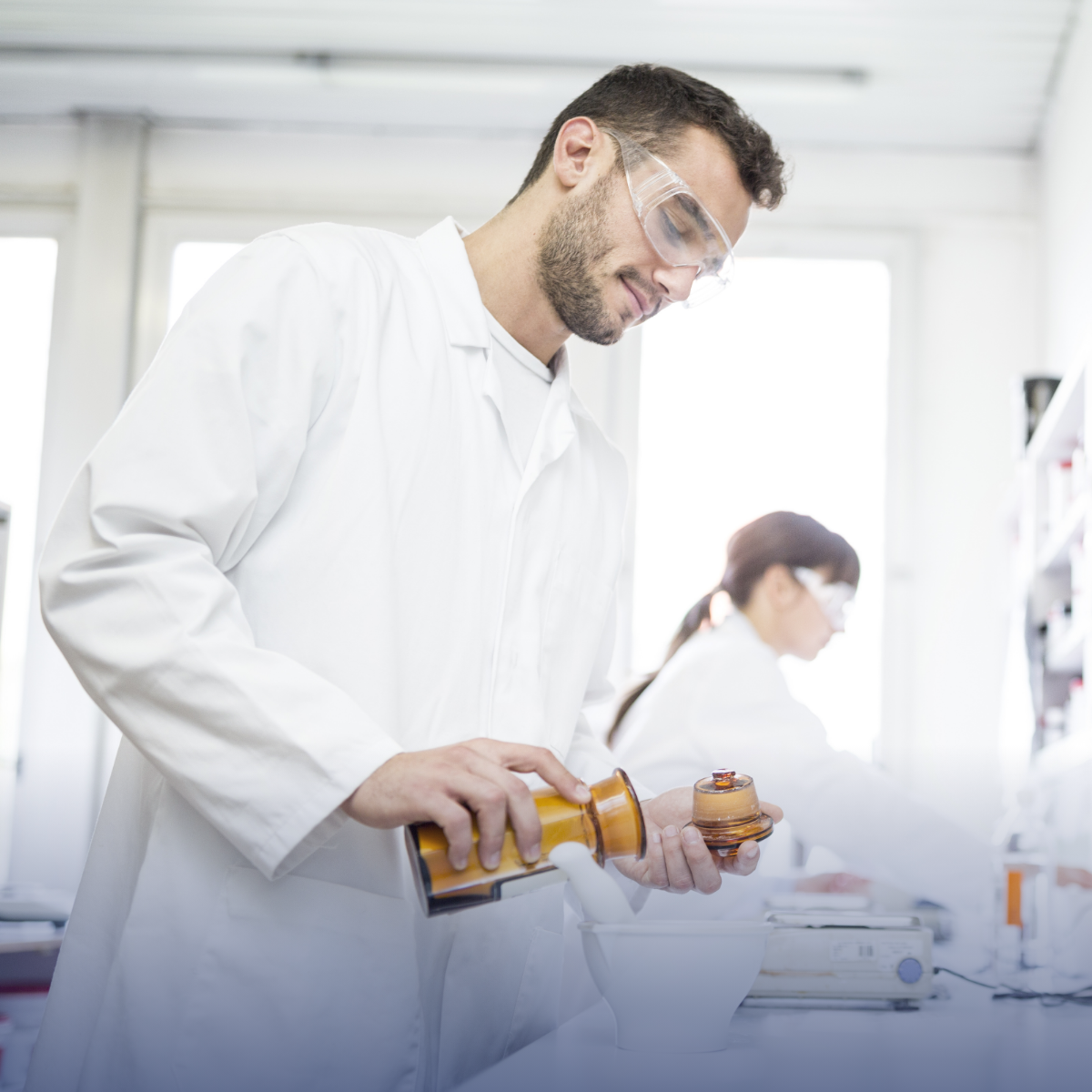
NPD (New Product Development)
At PharmaNZ, we offer a structured New Product Development (NPD) process to turn your supplement concepts into market-ready products. Our expert team guides you through every stage, supporting your formulation, packaging, and manufacturing requirements, with our partnership approach.
Scoping (1–2 weeks)
Start by providing us with a completed Product Technical Brief, followed by a collaborative discussion to define the project scope and formalise your NPD contract.
Project Initiation and NPD Phases
(4–8 weeks total, some steps may run concurrently)
Once the consulting contract is issued and the deposit is paid, we begin the development process.
- Phase 1 (2–4 weeks): We refine your formulation by considering ingredient sourcing, regulatory compliance, material specifications, and preliminary pricing estimates. Lab work ensures capsule or tablet compatibility before finalising the draft formulation. This can include product pricing feasibility analysis.
- Phase 2 (2–4 weeks): Packaging and component selection and label artwork creation are completed, with approvals required before production. Where appropriate, a Machine Trial Run can be conducted to assess manufacturability.
Project Completion
With the NPD phases finalised, your product is ready for formal quotation and first production. A final NPD invoice is issued, marking the completion of the NPD process.
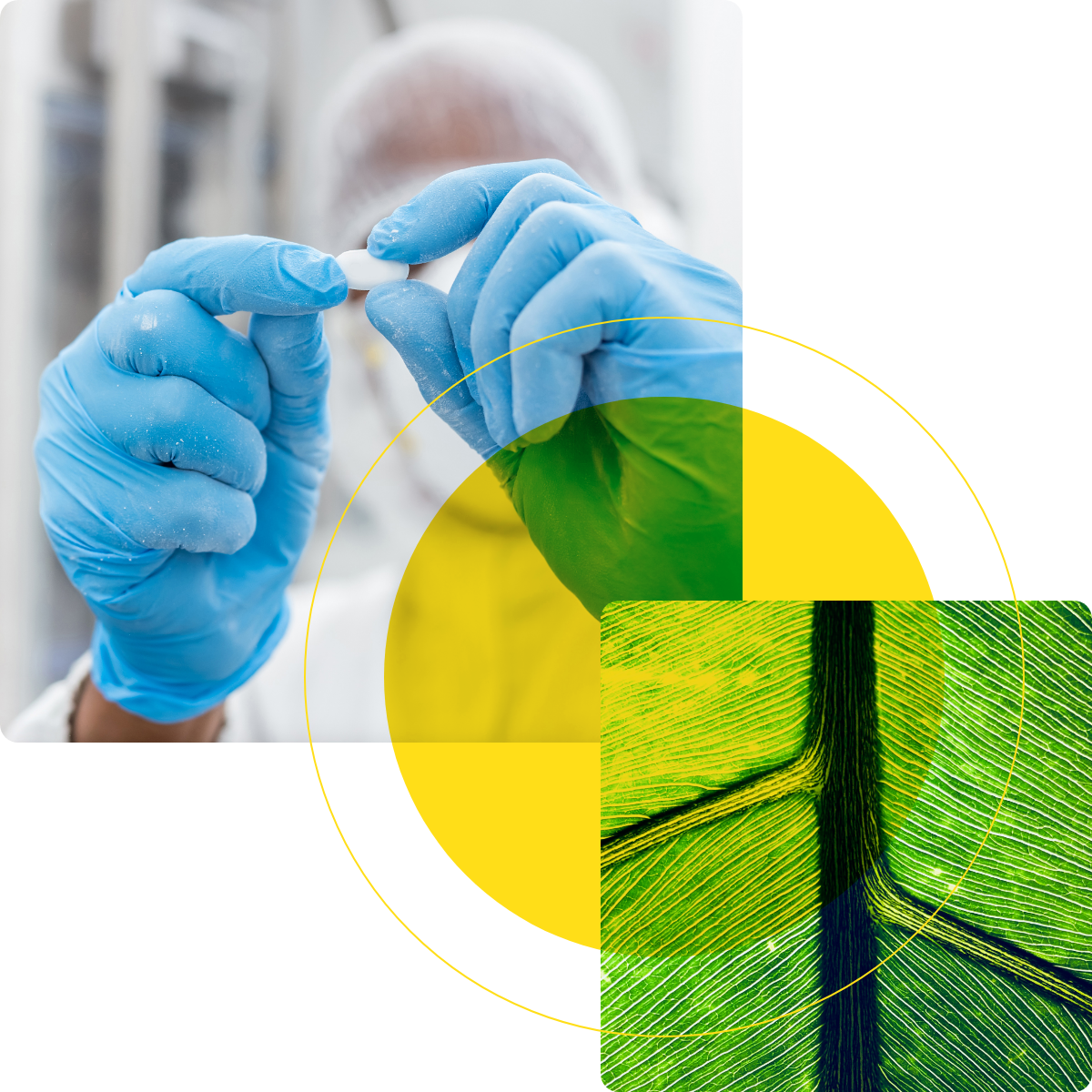
Pre-Production
(New Quotations and Reorders)
At PharmaNZ, our Pre-Production Process ensures a seamless transition from product development to full-scale manufacturing. Whether it’s a new or repeat order, we follow a structured approach to maintain quality, efficiency, and compliance.
- Formula & Specification Review: We assess your product formula and specifications for any updates, ensuring the latest raw material (RM) and component pricing is reflected.
- Formal Quotation & Order Confirmation: A detailed sales quote, including terms, conditions, and an estimated dispatch date based on RM and component lead times, is issued. Once the signed quote is returned and the deposit is paid, the order is confirmed and actioned.
- Procurement & Specification Finalisation: Any new RMs are allocated codes (see the documentation required). All relevant RMs, bottles, lids, labels, and packaging components are then ordered and lead times confirmed. Artwork must be reviewed and approved. The Bulk Formula & Specification (BFS) and Finished Product Specification (FPS) are finalised and signed off by the product sponsor.
Production Scheduling
Manufacturing is scheduled only when all materials and components have been received and logged into our Quality Management System (QMS), ensuring everything is in place for a smooth production run. Production delays are usually due to labels (design, approving and then printing) – the earlier this can be finalised the sooner the product can be manufactured.
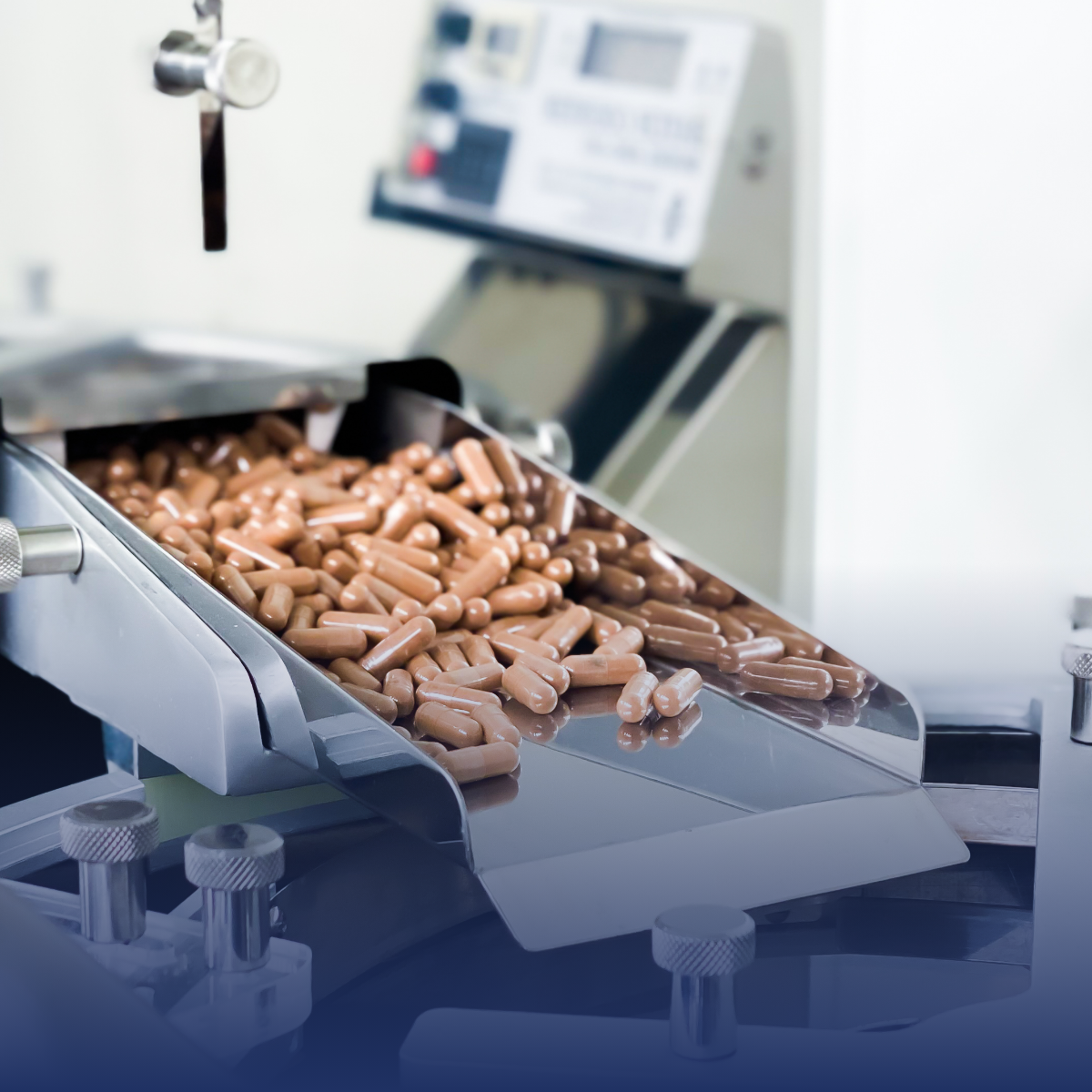
Manufacture and MOQs
3 week forward planning of the schedule allows time for Bill of Materials (BOM) to be built, the Assemblies (ASM) to be created and batch manufacturing (BMR) and batch packing records (BPR) to be created.
Once all docs are prepared and signed off, and all RMs and components are ready (released in the QMS), the product can be made (produced). Production is divided into important three steps (each of which must be signed off by Quality before proceeding;
- Dispense and blend
- Encapsulate/tablet
- Packing
The first three production runs are always considered ‘trial runs’ (where any small changes are made to ensure the product runs efficiently).
After the product is made, the required testing and sampling (if any) is completed, assemblies are closed, documents are reviewed, batch CoA’s are created and the Quality team formally release the product to the sales team, who action invoicing and dispatch.
Our Minimum Order Quantity (MOQ) depends on the product, but as a rough estimate, we don’t usually make less than 2,000 finished units (packs of 60’s) per run to start with. Economies of scale tend to kick in from 5,000 units per batch upward.
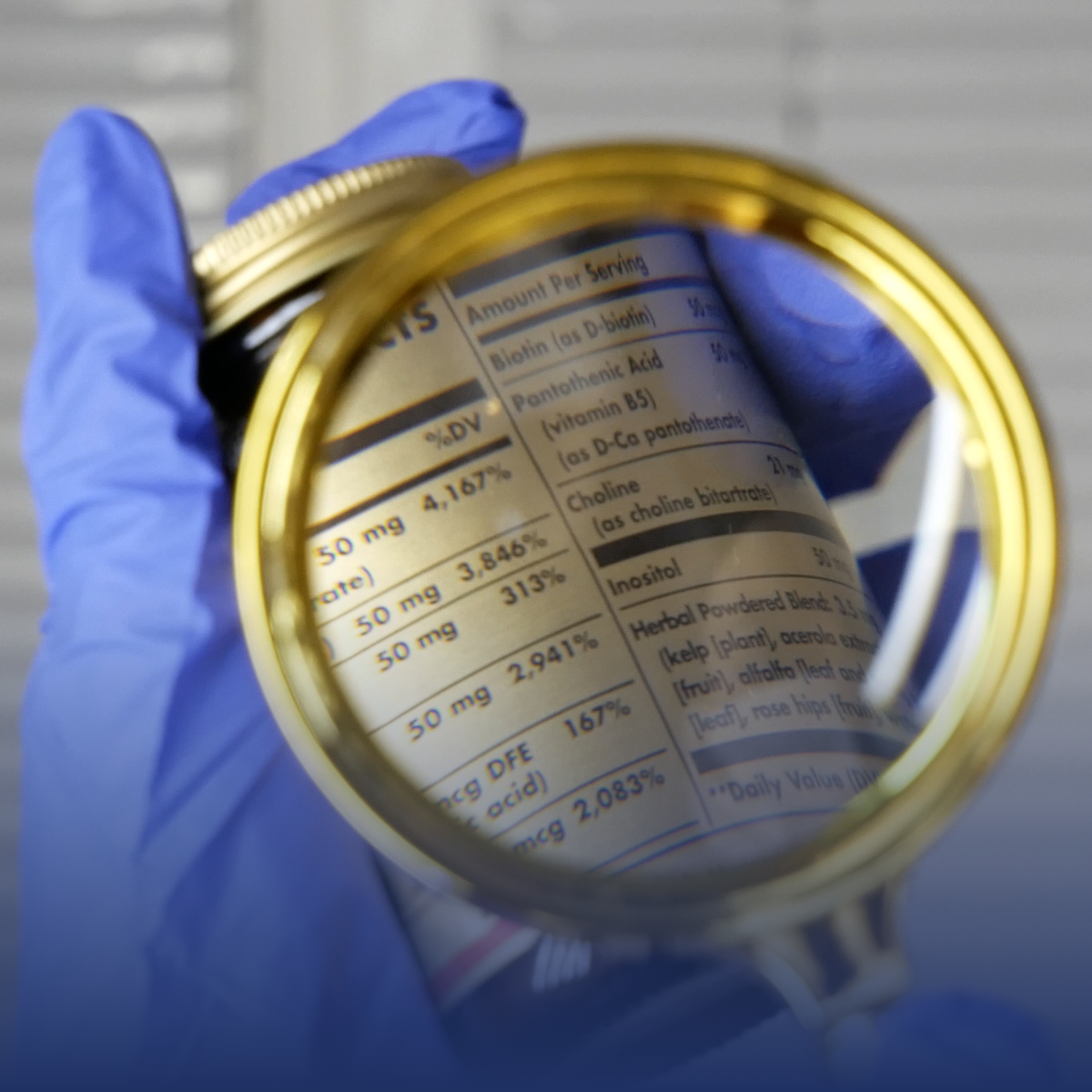
Documentation and Approvals
The cornerstone of good manufacturing practice (GMP) is quality documentation and at PharmaNZ we are passionate about producing top quality products. During the product developmemt journey, there are a number of documents that require either client and/or maufacturers sign-off. Here are some examples of important Process Documentation:
- Batch Manufacturing Records (BMR) and Batch Packing Records (BPR) – the instruction documents (bulk or finished) to ensure quality and compliance to procedures during production. Signed off by each appropriate department lead before and after production.
- Material Codes – Every RM has a code in our QMS (quality management system). New material supporting documents (certificate of analysis, country of origin, MSDS, product specification, allergen declaration, other relevant certificates ie animal, halal, organic etc) are required for every material.
- Bulk Product Specification (BPS) and Finished Product Specification (FPS) – Specification for each bulk product and/or finished (packed) product (includes components, materials and any necessary or requested testing requirements).
- Artwork – Customer supplied label artwork must be reviewed and approved by PharmaNZ before printing. We can provide guidance for local and export markets where appropriate or refer to one of our regulatory consultant partners if necessary. Creating a compliant label is usually the rate limiting step for production.
- Certificate of Analysis (CoA) – Document summary of ‘what was made’, including any testing or product parameters relevant to the specific batch.